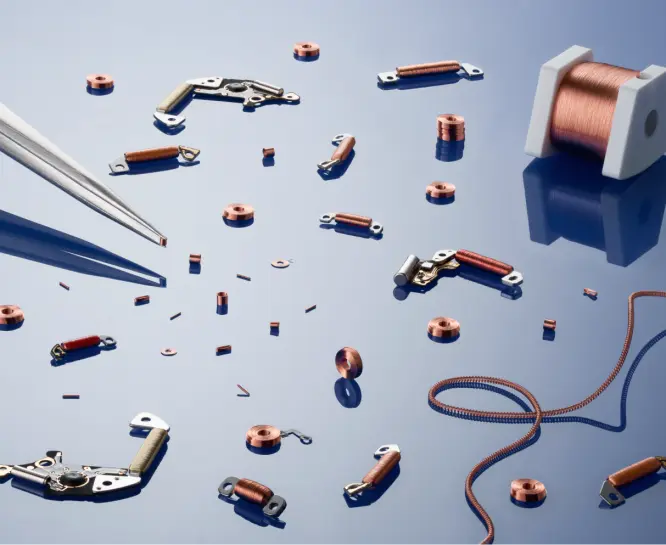
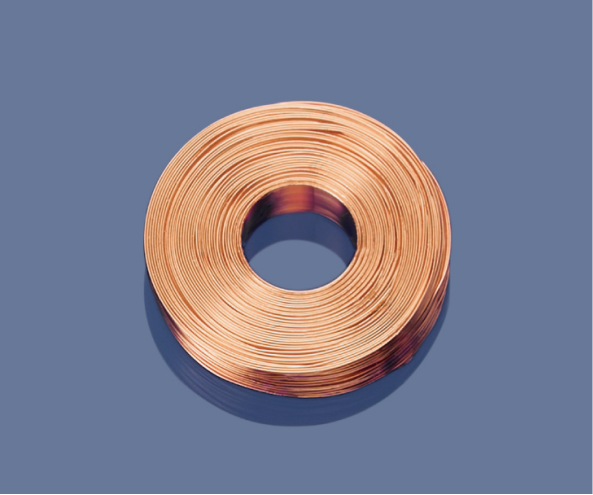
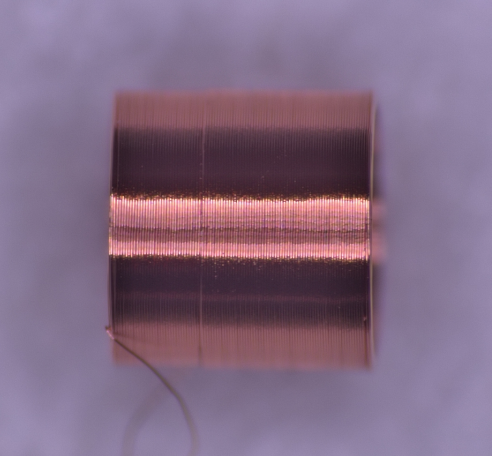
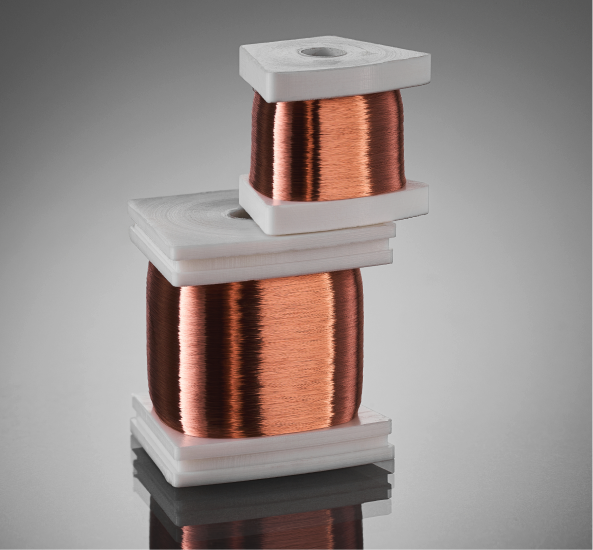
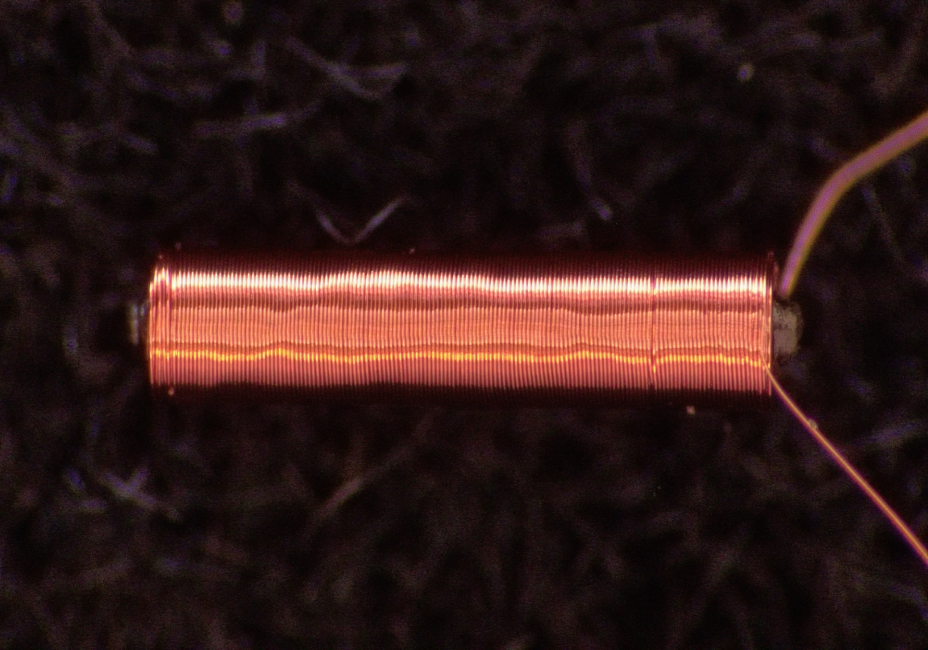
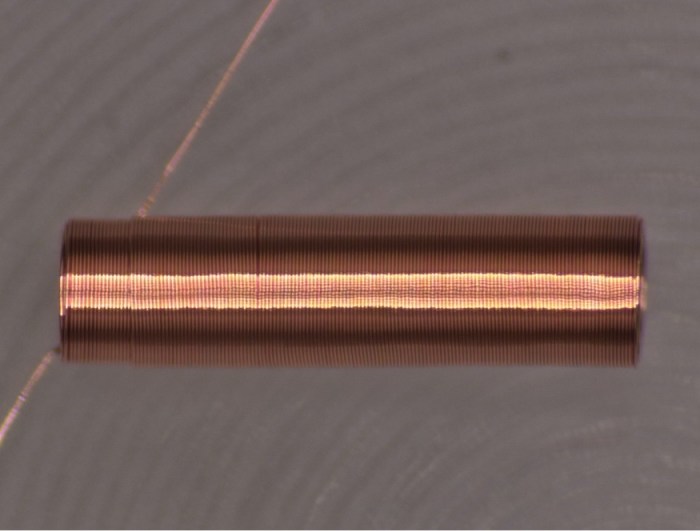
Microcoils
Microcoils are crafted for high precision and reliability in industries like medical devices, electronics, and sensors. Designed to meet strict quality standards, these coils ensure optimal performance in compact, complex applications.
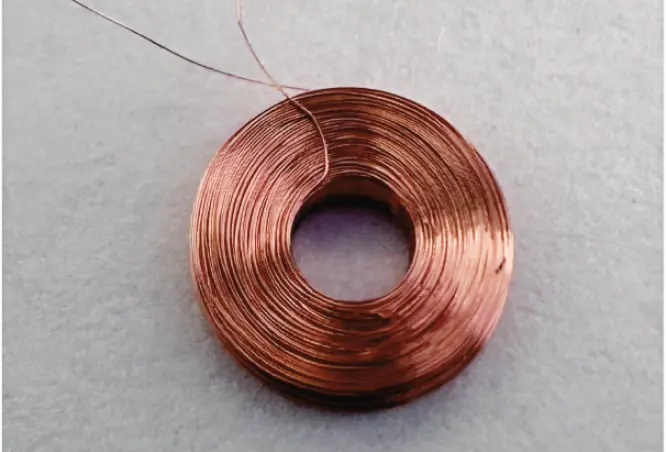
MICROCOIL
A microcoil is a tiny electromagnetic coil used in applications requiring compact size and precise magnetic fields.
They are used:
→ in MRI for imaging specific body regions;
→ in MEMS as sensors or actuators;
→ in miniature transformers, inductors;
→ and other space-constrained components needing precise inductive properties.
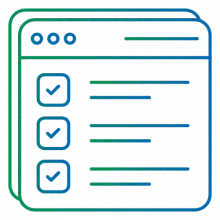
KEY FEATURES
- Lightweight and compact design
- High efficiency and precision
- Customizable configurations to meet specific requirements
- Exceptional performance in diverse environmental conditions
- Wide range of applications across industries
- Rigorous quality control for consistent performance

APPLICATIONS
- Medical devices and implants
- Wireless communication systems
- Automotive electronics and sensors
- Renewable energy systems
- Aerospace and defense systems
- RFID devices and NFC technology
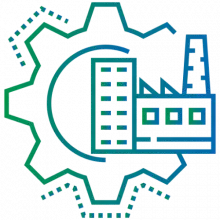
INDUSTRIES
- Medical devices
- Electronics
- Automotive
- Aerospace
- Industrial automation
- Telecommunications
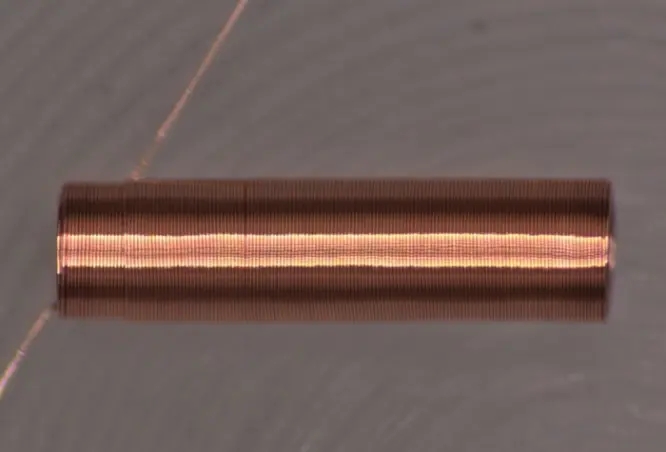
AIR MICRO COILS
We specialize in winding copper wire to astonishingly fine dimensions, achieving sizes as delicate as 10 µm. Our portfolio of air core coils includes a wide variety of shapes and configurations, allowing us to provide tailored solutions to meet the specific needs of our customers.
From traditional cylindrical coils to unconventional geometries, such as elliptic, helical, and flat-wound designs, we offer a comprehensive range of options to suit diverse applications and requirements.
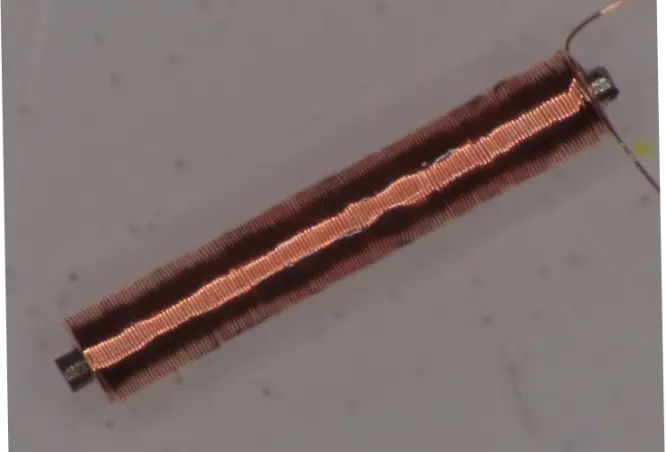
MICRO COILS ON CORE
Each microcoils on a core is precision-wound using modern techniques, guaranteeing optimal electromagnetic performance. These coils are designed for high precision and stability in demanding applications, making them ideal for sensors, medical devices, and intricate electronics.
With customizable designs to match your specific requirements, they offer optimal efficiency and reliability in complex systems.
CORE TYPES
Microcoils are precision-wound utilizing advanced winding techniques to ensure high electromagnetic efficiency and minimal core losses.
We offer an array of core materials:
→ magnetic cores for maximized magnetic permeability,
→ ferrite cores for high-frequency stability,
→ polyimide cores for superior mechanical flexibility,
→ non-magnetic cores for optimal electromagnetic shielding and interference reduction.
Magnetic cores are typically made from materials such as iron, steel, or ferromagnetic alloys and are widely used in transformers, inductors, and electromagnets due to their ability to efficiently concentrate magnetic flux and enhance magnetic performance. They exhibit strong magnetic properties, including high magnetic permeability and saturation flux density.
Ferrite cores are composed of ceramic compounds made from iron oxide (Fe2O3) and other metal oxides, such as manganese, zinc, or nickel AND are commonly used in RF transformers, inductors, and high-frequency circuits due to their low electrical conductivity and high magnetic permeability at high frequencies. Despite their ceramic composition, ferrite materials exhibit strong magnetic properties and high magnetic permeability, especially at high frequencies.
Non-magnetic cores are made from materials that are not susceptible to magnetic fields, such as plastic, ceramic, or glass and are used in applications where magnetic interference must be minimized or where magnetic properties are not required, such as in high-voltage insulation, mechanical support, or structural components.
They are electrically insulating and do not exhibit any magnetic properties.
Polyimide tubes serve a dual purpose as both the core and the insulation for the micro coil. Micro coils wound on polyimide tubes find applications in various fields, including medical devices, aerospace systems, telecommunications, and consumer electronics. They are commonly used in sensors, actuators, transducers, and other miniature electronic components where compact size, high performance, and reliability are essential. The diameter, length, and thickness of the polyimide tube can be customized to meet specific design requirements. This allows for the creation of micro coils with precise dimensions and electrical characteristics tailored to the needs of the application.
Custom bobbins are precisely engineered structures made from materials such as plastic, ceramic, or metal. They are designed to provide a stable and uniform platform for winding the micro coils. They can be manufactured to specific dimensions, shapes, and configurations to meet the requirements of the application.
Custom bobbins provide insulation and protection for the micro coil windings, preventing electrical short circuits and mechanical damage. Additional insulation materials, such as varnish or epoxy resin, may be applied to further enhance the electrical insulation and mechanical strength of the coil.
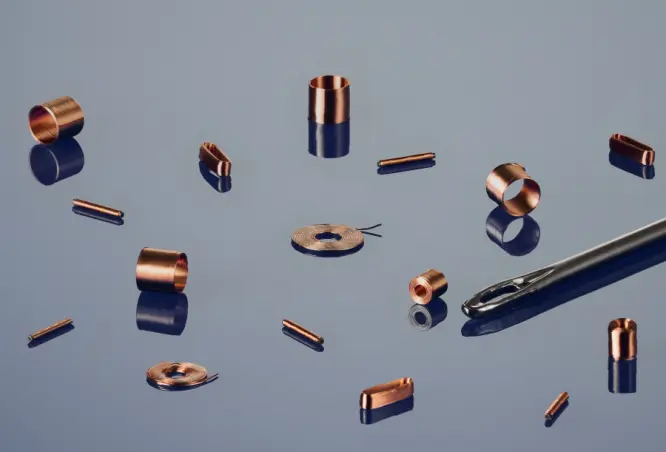
MICRO coils SPECIFICATIONS
Wire Diameter: from 10 µm to 100 µm.
Coil Diameter: from 75 μm for micro coils with magnetic / non-magnetic cores and from 200 µm for coreless micro coils.
Material: from copper or other highly conductive materials to ensure efficient electrical performance.
Coil Geometry: from traditional spiral or helical coils to more intricate geometries, wound on a core or a bobbin.
Environmental Considerations: some micro coils may have special coatings or encapsulation to protect them from environmental factors such as moisture, temperature extremes, or mechanical stress.
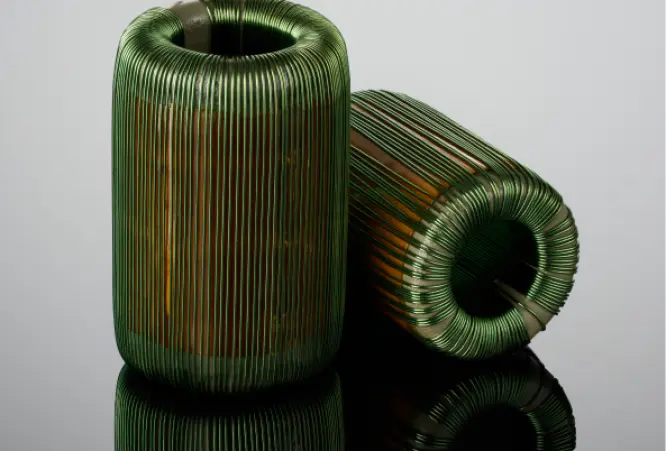
Toroidal coils
Our toroidal coils feature a ring-shaped core, engineered to enhance magnetic flux density and minimize electromagnetic interference. Precision-wound to ensure optimal inductance and efficiency, these coils offer low core losses and high performance in compact spaces.
The toroidal shape minimizes leakage flux and enhances magnetic coupling, ensuring stable performance in demanding electronic and electrical systems.
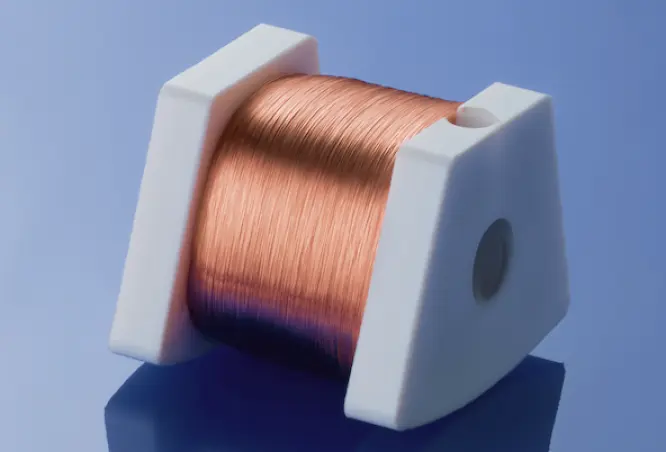
micro coilS potting
Micro coils with potting are encapsulated in a protective resin, providing enhanced durability and environmental protection.
The potting process ensures superior mechanical support and insulation, safeguarding the coils from moisture, vibration, and thermal stresses.
This encapsulation enhances mechanical stability and ensures consistent electrical performance and longevity in challenging and high-reliability applications.
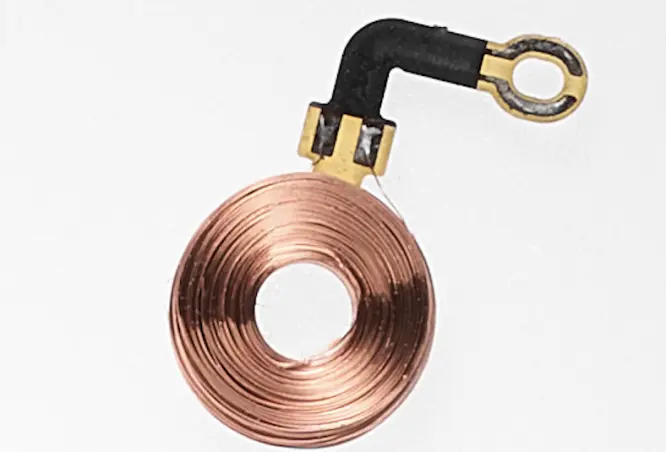
assembly of complete coils modules
The assembly process for complete coil modules involves integrating high-precision coils into fully assembled, functional units. This process ensures meticulous alignment, secure connections, and reliable operation, optimizing each module for its intended application.
Each module is designed to offer seamless integration and reliable operation in various applications, from medical and industrial systems to sophisticated electronic devices.
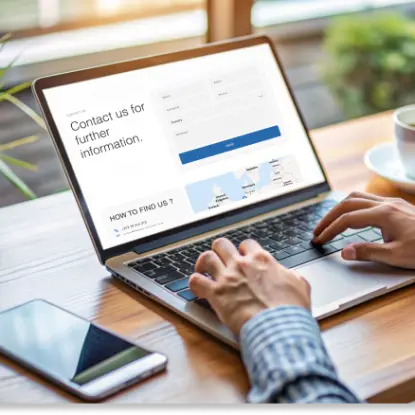
Custom requirements - tailored solutions
We deliver customer-specific solutions that maximize efficiency and results, tailored precisely to each challenge.